Connecting The Dots: Technical Inertia
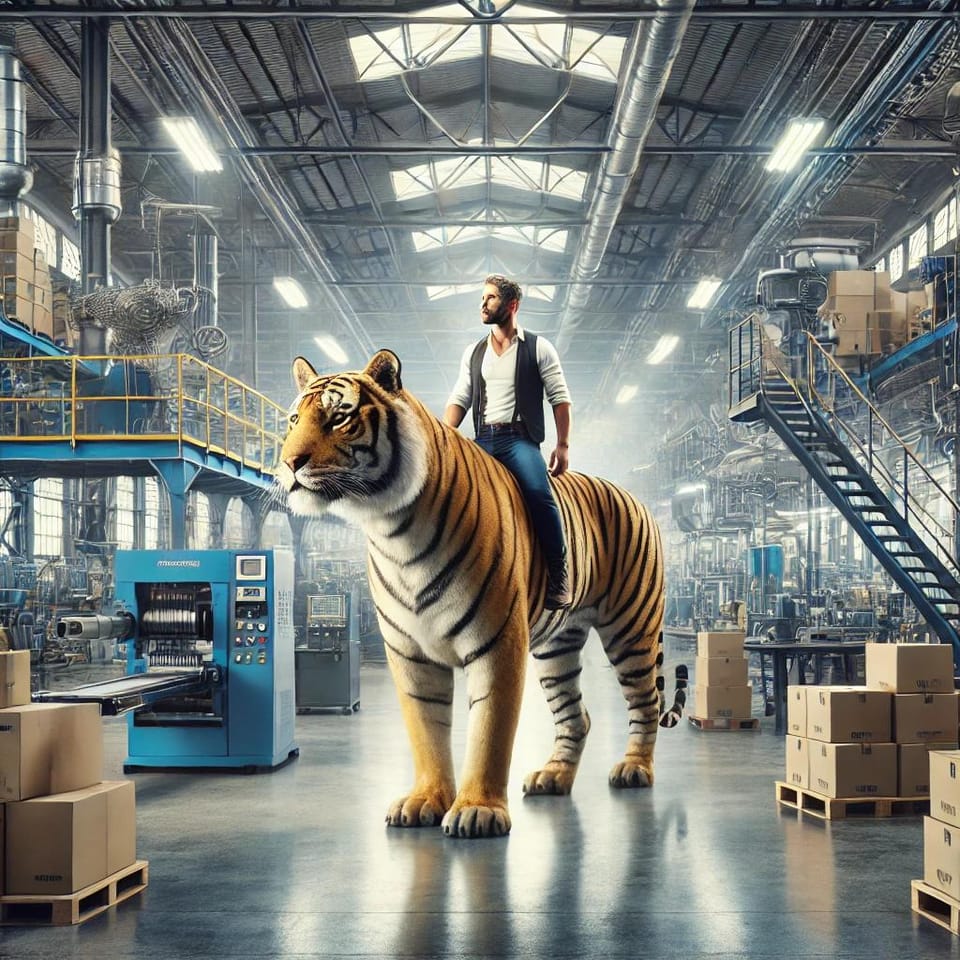
The manufacturing of complex mechatronic medical devices relies heavily on automation. Automation delivers product quality at speed as a process subject to lot testing and in-process testing. Minimizing variability in manual operations enables sophisticated analyses of process variability.
With increasing in-process automation comes design momentum — changes become tedious and expensive, and imply risk. Product component changes may require new ways to precisely manipulate small parts. Scaling automation changes from a small prototyping line to the high volume lines may reveal problems that quickly scale from small numbers on the prototyping line to losses of large lots on the production lines. In the worst case, problems may present in products shipped to customers.
As successful companies scale manufacturing operations to serve market expansions, the technical inertia increases. It becomes difficult to make major product changes. "Who rides on the back of a tiger can never dismount" - Chinese proverb
Companies intending to compete with Insulet in the disposable patch pump segment intend to minimize the impact of technical intertia by using two or more assemblies to compose their patch pump. The Roche Solo is an example. In this case, the complex mechatronics are durable and the fluid path is disposable. Scaling the fluid path module is easier than scaling the mechatronic module — the fluid path module is uncomplicated and unlikely to evolve over time. A second example is the AMF (Tandem Diabetes) patch pump. The fluid path component has fewer articulating parts than the durable component.
A concept advanced by Aita Bio Inc. is an attempt to bring a disposable patch pump. The Aita Bio Inc. concept utilizes a MEMS pump — design inertia is implied. Scaling the concept taught in their published patent applications will be tedious, and expensive. Process changes while scaling manufacturing would be capital-intensive.